PIPING ENGINEERING (Course Duration 3 Months / 1 Months)
Codes, standards, and specifications from ASME, ANSI, ASTM, API, NACE, MSS, AISI, AWS, AWWA, and PFI. Material science of various piping materials, including carbon steel (CS), alloy steel (AS), stainless steel (SS), Hastelloy, Inconel, copper-nickel, and more. Different types of pipes such as seamless, rolled ERW, rolled EFW, and spiral welded pipes. Fittings including long-radius elbows, short-radius elbows, 45-degree elbows, equal tees, reducing tees, eccentric and concentric reducers, reinforcing saddles, weldolets, sockolets, threadolets, elbowlets, latrolets, and welding bosses.
Various types of flanges, including weld neck, slip-on, socket weld, blind, lap joint, reducing, and orifice flanges. Different types of valves like gate, globe, ball, butterfly, plug, needle, four-way, three-way, non-return, angle, PSV, PRV, FCV, TCV, and level control valves. Welding procedure specifications (WPS), WPQR, and WPQT.
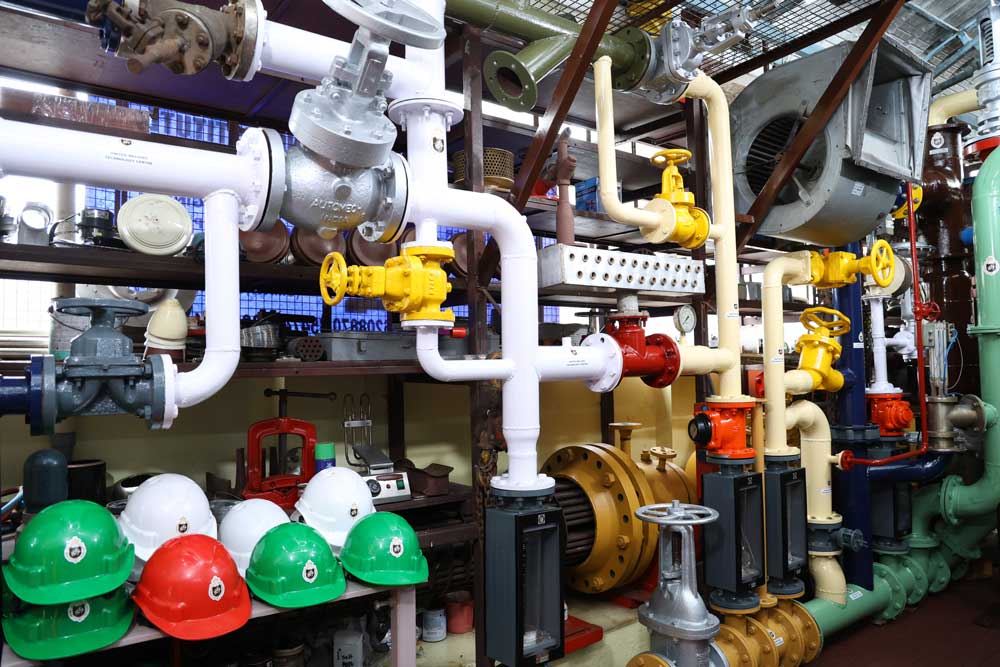
Fabrication and erection of steel structural drawings for pipe racks, pipe trenches, pipe sleepers, platforms, ladders, handrails, pipe supports, and more. Erection drawings for static and rotating equipment, such as columns, vessels, heat exchangers, condensers, fin fan coolers, reactors, absorbers, fractionators, flare stacks, and relief system stacks.
Method statements for pre-fabrication, site fabrication, and erection of piping systems for underground and above-ground installations. Method statements, job safety analysis, risk assessments, total safety task instructions, rigging studies, and plans for heavy lifting and erection of steel structures, pressure vessels, and various rotating equipment.
Plot plans, site plans, general arrangement drawings, isometric drawings, spool drawings, flow diagrams, and P&IDs (piping and instrument diagrams).
Pre-fabrication, site fabrication, and installation of various piping systems, including utility systems, fuel gas systems, process systems, flare systems, relief systems, firewater systems, jacketed piping systems for sulfur and asphalt lines, cement-lined piping systems for cooling water and seawater, and steam tracing.
Line checking as per test pack, ISO drawings, P&ID, ITP (inspection & test plan), pipe internal cleaning reports, NDE reports, flange face inspection reports, bolt torquing & tensioning reports.
Issuing punch lists, confirmation of punch clearance, and submission of test pack approval for Ready for Test (RFT).
Hydrotesting, pneumatic testing, visual testing, chemical cleaning & pickling, piping system draining, flushing, pigging, air blowing, steam blowing, and system acceptance for inert gas filling and handover to commissioning.
Safety
PPE (personal protective equipment), safety equipment and tools, safety orientation & induction training, toolbox talks, working at height, confined space entry, excavation, power tools, hot work, heat stress, electrical/mechanical lock-out/tag-out, and emergency rescue plans. Mobilization of temporary site facilities, tools, and equipment.
Documentation
Site observation reports, material approval requests, non-conformity reports, daily progress reports, daily manpower reports, machinery stock register, piping fit-up & weld visual reports, rotary & static equipment alignment reports, line history sheets, piping site fabrication and installation measurement summary sheets, mechanical clearance of piping loops, hydrotesting, and pneumatic testing reports.